Thinking Outside the Box with Modular Design & Construction
By: Jennifer Hocherman, AIA, LEED AP, Beverly Architect
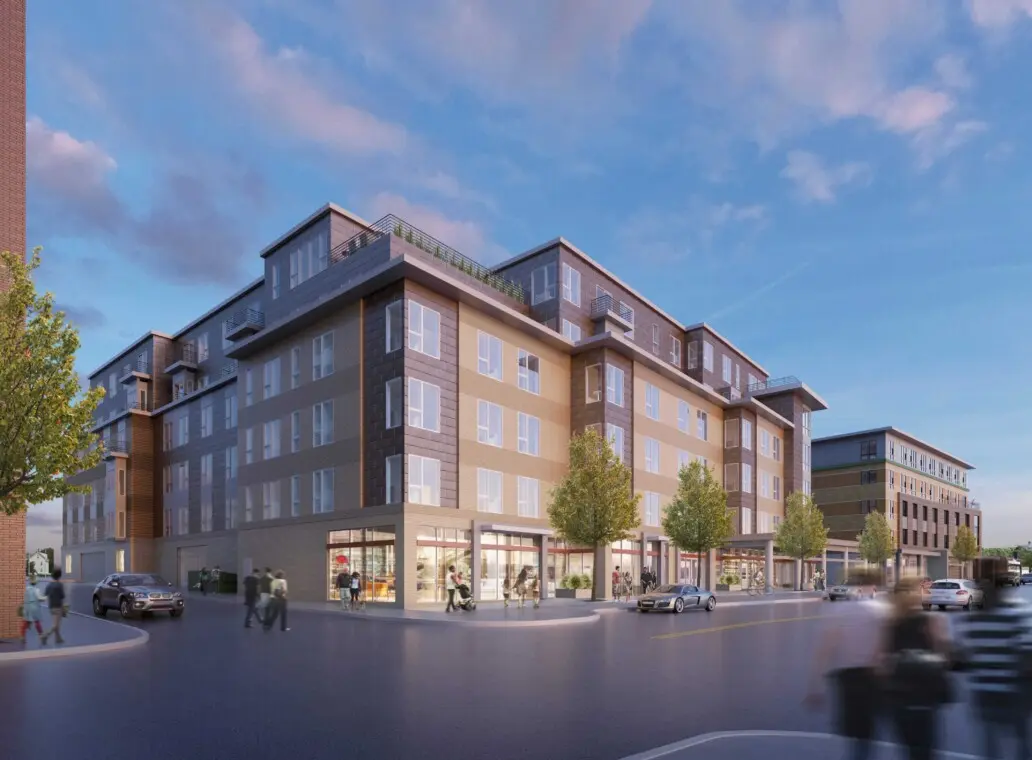
Community innovation is thinking outside the box to provide solutions to challenges a community may face. In this case, the growing city of Beverly and communities north of Boston have a lack of housing for those commuting into the city and working on the North Shore. In addition, there’s a shortage of skilled laborers supporting the construction industry in Massachusetts.
Canvas, a mixed-use multi-family project totaling 126 units was designed by SV Design and developed in downtown Beverly, Massachusetts by Beverly Crossing. This project adds a housing option for the community and utilizes local companies and laborers to work on the project. Canvas is located a few blocks from the Beverly Depot Commuter Rail Station and adjacent to one of Beverly’s primary civic centers.
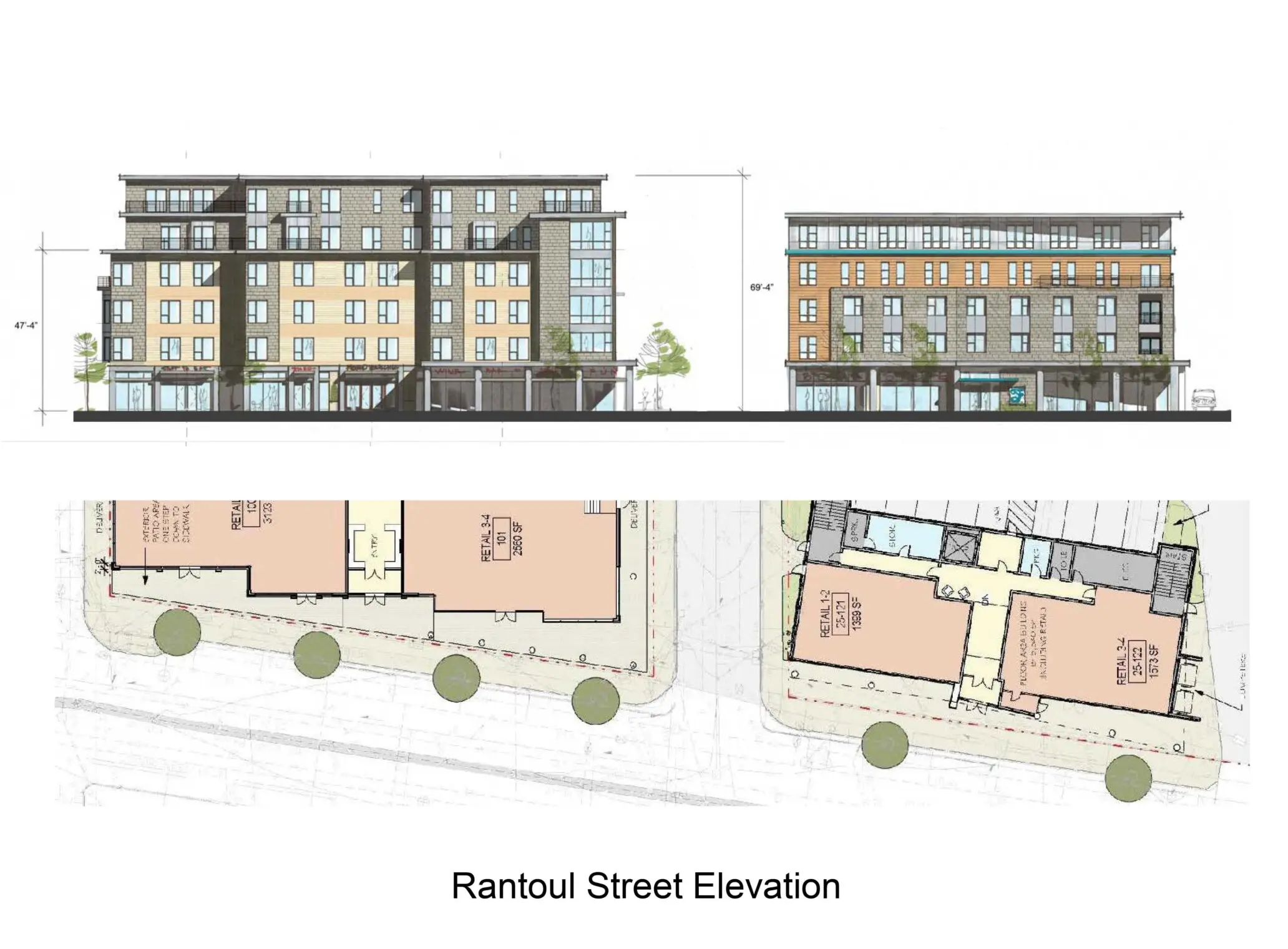
SV Design, the architect and interior designer for the project, designed two, six-story buildings with 126 units with the first level of each building to include retail spaces. SV Design and Windover Construction reviewed the timeline and went back to the drawing board after the traditional methods of construction for these buildings would not allow for this project to be completed by the anticipated deadline. In order to meet the desired schedule, a modular construction approach was adopted, however the design was not sacrificed. This approach allowed for a reduction in project cost and construction waste. The efficiency with modular construction comes from preset design pieces and a repetitive kit of parts. Our design had building setbacks with undulations and kinks throughout the façade.
Working closely with the modular manufacturer, SV Design made adjustments to the steel layout to align with point loads created by the boxes and adjustments to select unit layouts to fit within the parameters. The Mechanical, Electrical, and Plumbing (MEP) team had to adjust layouts to accommodate the stacking and alignments necessary for placement. The reconfiguration and coordination process added three months to the design and documentation schedule but did not delay the start date.

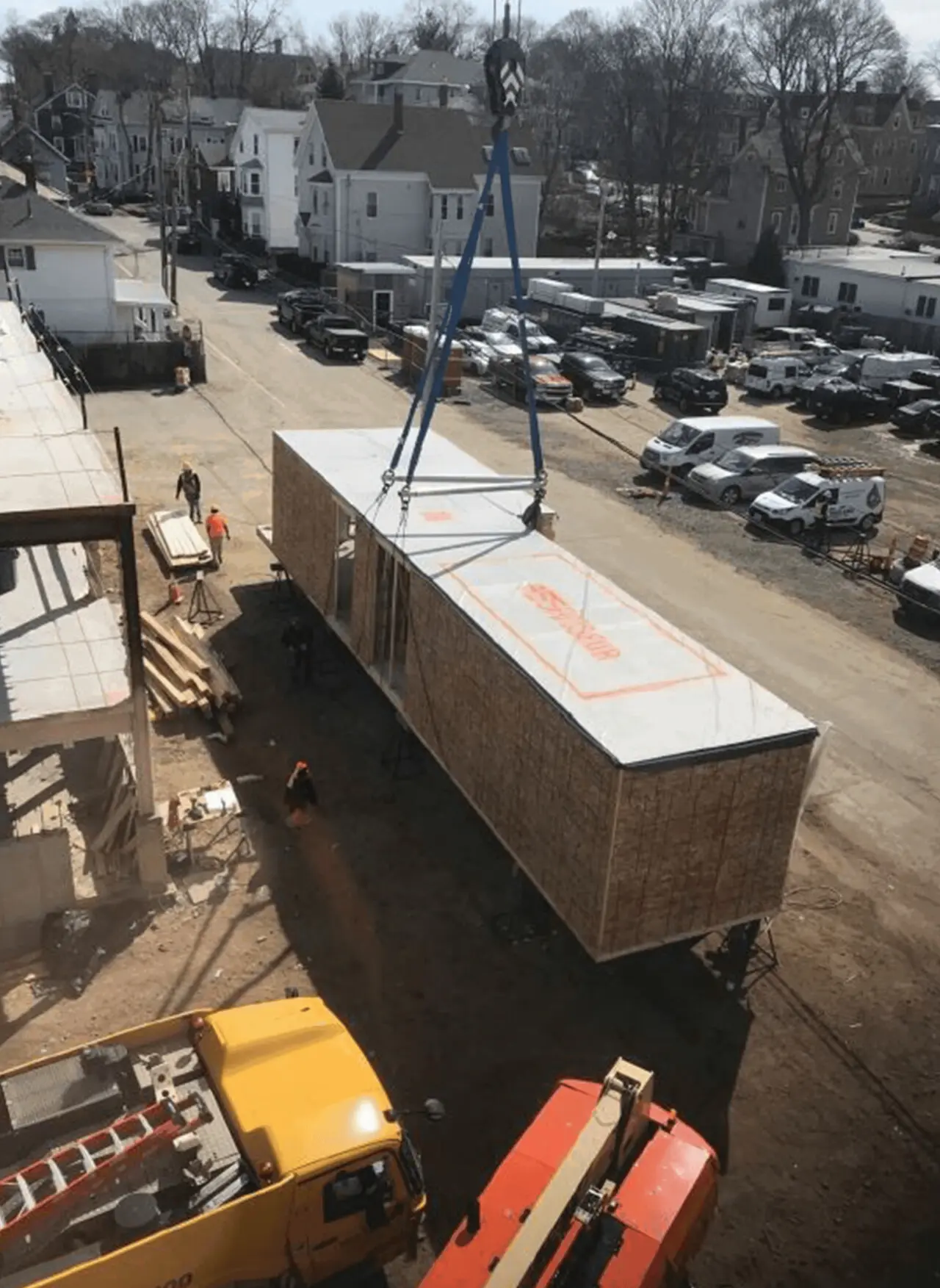
While awaiting steel and modular shop drawings, the old car dealership on the lot was demolished and the new foundations were poured. SV Design successfully met the demands of this unique process; shop drawings and finish specs were completed much earlier than in a traditional method of construction. Once the boxes arrived on site, the buildings went from being empty, two-story podiums to full framed, six-story buildings in two months. Not only were their sheets constructed, but they were finished with gypsum, millwork, and sprinklers. Over the next three months, field connections of the pre-located MEP systems were made and exterior finishes applied.
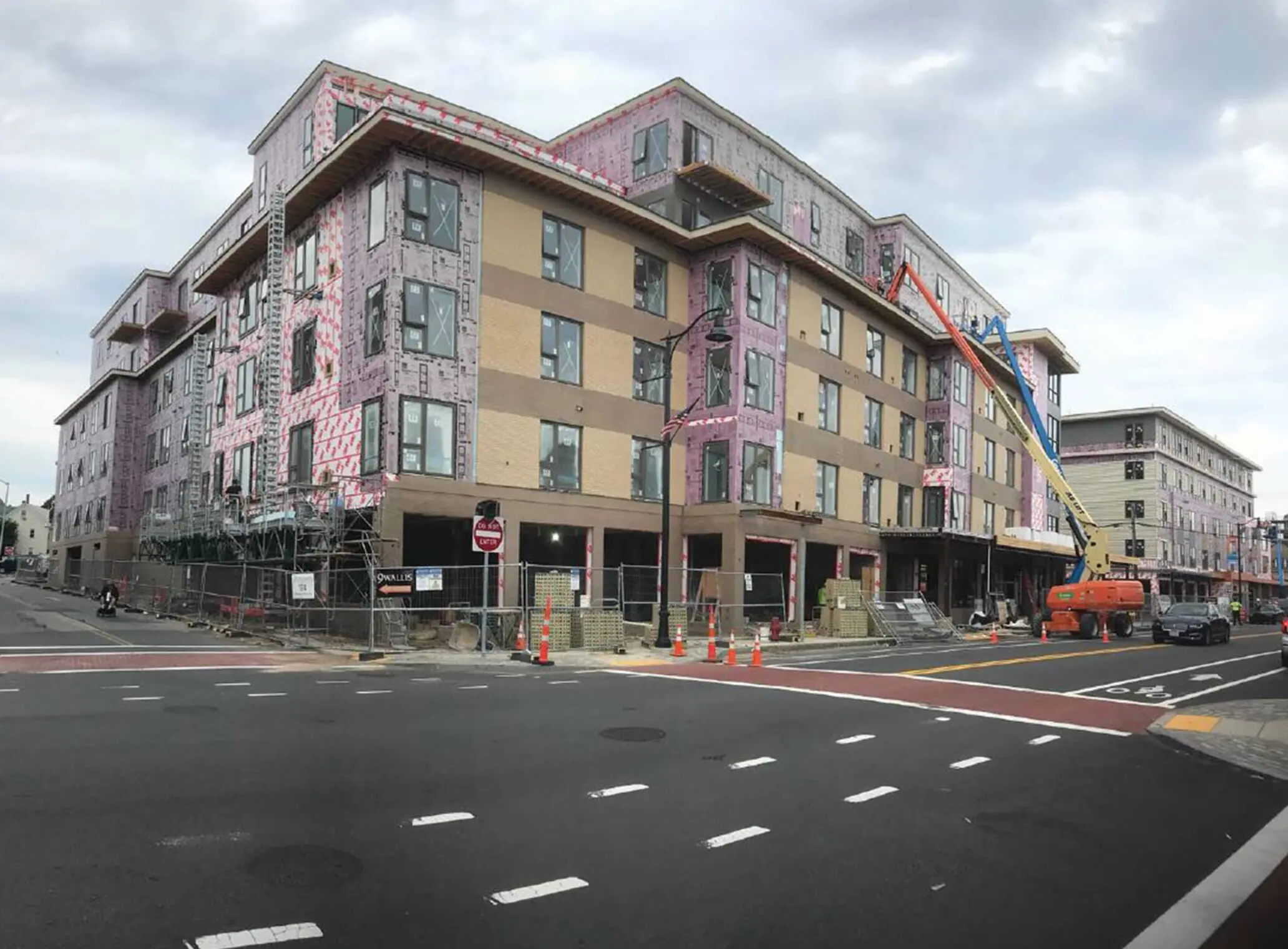
Canvas was completed in the Fall of 2019 and now has occupancy. It’s hard to believe it was a modular building, since it does not have the stereotypical modular box look and symmetry that you may expect from this type of construction. Using the modular process allowed a shortened construction schedule in a time when finding enough sub-contractors to be on site was difficult. The approach of Canvas’ modular design and construction was an innovative way to overcome challenges and meet objectives. The finished project is a testament to thoughtful and functional design.